Smooth outsourcing of internal logistics always supports some value stream in business and enables it to function well. But how is it developed and what steps are taken when it is decided to outsource internal logistics? HUB Logistics’ business directors Janne Marttila and Mikko Heinilä discuss the matter.
With internal logistics, you can at best develop business and the company’s main process. Then it creates an opportunity to develop the value stream it serves and gives the next stage the opportunity to develop forward.
– When internal logistics is outsourced, our task is to plan it so well that the user doesn’t have time to think about it. Then it creates opportunities for the development of the entire operation, say Janne Marttila and Mikko Heinilä, who are business managers of internal logistics at HUB logistics.
Outsourcing of internal logistics starts with joint planning
The development and outsourcing of internal logistics has clear benefits for production and operations. The progress of the development process depends entirely on the current situation, and therefore the mapping of the initial phase plays a big role.
If the factory already exists, the current premises will easily meet internal logistics and may create limitations for logistics outsourcing and production development. For example, production does not need high spaces, but logistics and storage need space upwards.
– If you get to do and plan internal logistics right from the start, you should build the warehouses close to the production line. In the warehouse, the rooms are higher and the temperature is cooler than the production rooms.
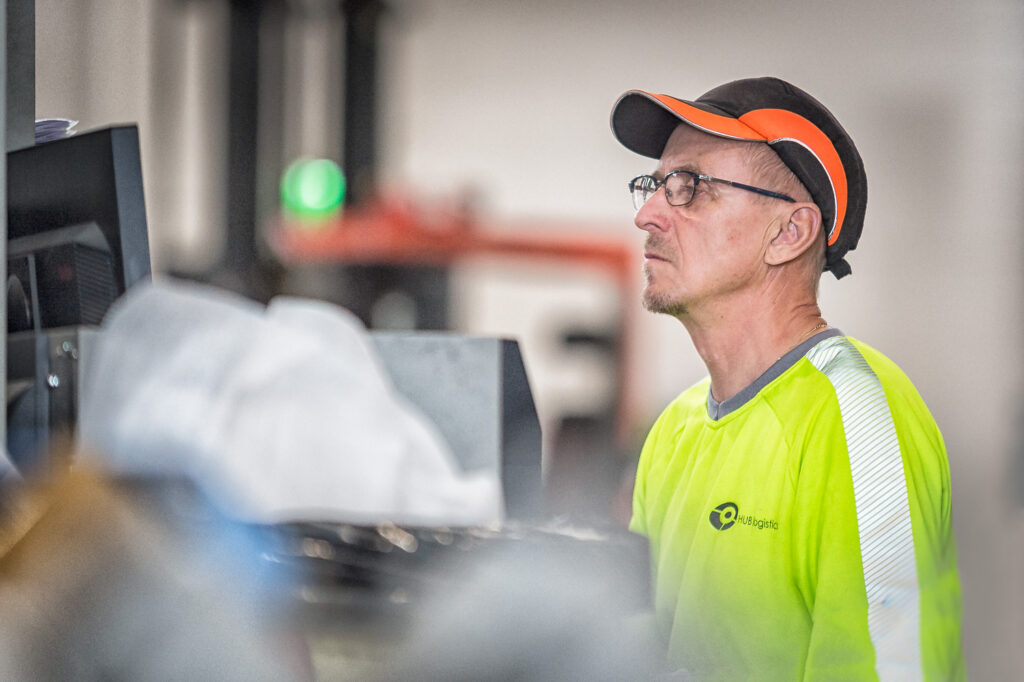
When outsourcing internal logistics, you must understand the customer’s needs
Basic planning is done together with the customer and HUB Logistics experts. In general, the customer’s production line states the wishes for how and with what response times the parts are delivered.
– In internal logistics, it is important to consider the IT systems of the house. Everyone who is part of the internal logistics team has some kind of device at their disposal to keep in touch with the systems. Information about needs and completed work moves through a computer, tablet, smartphone or voice control, Janne Marttila says.
According to Mikko Heinilä, in “building up” the internal logistics, the customer’s needs must first be understood, as in many other activities. Before planning internal logistics, you need to know the strategy and the aspirations of the vision: where does the customer aim to succeed in the future? Then we start customizing the service.
– Internal logistics and its outsourcing can be implemented in many ways and there are several solution options. It is essential to figure out where to succeed. Then we know which solutions can be used to support the goal.
– The initial stage of internal logistics planning is strict data processing and job research. That is, how much time does each step take and how do you reach the most effective end result at different points?
In terms of concrete things, we always start to find out about the customer’s needs: what kind of facilities are in use, at what frequency are the goods delivered and how are they delivered, so that in the next step there is no need to search and retrieve anything?
– Then it’s time to optimize the traditional issues of logistics outsourcing: where to drive and when to drive, how to store and where, how internal logistics can also handle waste management on behalf of the end customer and so on, Mikko Heinilä lists.
In logistics outsourcing, the customer’s concerns are heard and resolved
When work has been done in the same way in a factory or company year after year, getting the pace of development started can sometimes be behind the work. Customers may show resistance to change because it has always been done this way. But when the first project is successful, according to Janne Marttila, the track is open to credibility. When you dare to make changes, there will also be positive effects on production.

Mikko Heinilä adds that customers think a lot about transparency and whether contact with operations will be lost if internal logistics is outsourced. Today, however, digitality brings infinitely good medicine to it. With it, it is possible to report and show the customer a real-time situational picture.
– Transparency is one of the most important things in outsourcing internal logistics. And the second is that outsourcing is built on the basis of understanding the customer’s will and strategy.
– The customer may wonder if the change may be too big and difficult. Of course, euros and the profitability of outsourcing are also calculated. And the customer wonders how it really works. All of these are already reviewed together in the initial stages, as long as the discussion connection is established, says Mikko Heinilä.
Cooperation in the outsourcing of internal logistics starts with a survey of the current situation
– We usually do an on-site production tour at first, where we get a complete picture of the current situation of production and logistics with our own eyes. Of course, we also talk about our references and get to know our units together, Janne Marttila says.
– We listen to customers and find out production goals. They can be, for example, that they want to increase production by ten percent, or that they want to renew the paint shop and that will bring changes.
In the initial phase, a “process narrative” is made for the customer, i.e. a summary of the current situation, in which we go deeper into the biggest development items and tell the three most important things that HUB logistics would do differently and which we would start developing.
– When the discussion continues and a partnership emerges, the next task is a more detailed work study, the kind of which has rarely been done in Finnish companies in terms of internal logistics. Then we will know how long the work phases related to internal logistics last, how much can be achieved with the current system and how ergonomics can also be developed. The customer then makes a decision about what they can do themselves and where we can offer our help.
– We prepare a phased plan for the smoothness of the ramp-up, and at the same time, the adequacy of the client’s resources and the schedules are defined. We do a lot of these things, but outsourcing internal logistics is usually the first time for a customer. That’s why at the beginning we go over everything the change means and requires. At the same time, of course, we will tell you what it enables.
– After that, the determination of the interfaces begins: which things belong to us, which to the customer and how the interfaces work.
The cooperation is based on mapping the current situation, listening to the customer and mapping the production goals. Understanding the customer’s needs is a decisive factor in planning and implementing outsourcing.
Janne Marttila, Business Area Director
Competence, experience and flexibility
HUB Logistics has experience in dozens of customer projects where it has been possible to further develop the customer’s logistics. They have achieved savings and qualitative improvement.
– We also dare to go boldly towards something new. We don’t always rely on the good, old and reliable way, but we look for new implementation methods that can handle things even better, says Janne Marttila.
– We have top-notch, experienced people at work. We constantly train new experts with internal training and by employing those who have finished their work. With it, we learn new things and guarantee continuity.
Also on the IT side, we can strongly support the customer in internal logistics solutions, and we are at a very good level in warehouse automation, Janne Marttila lists.
Mikko Heinilä sums up that know-how, experience and flexibility are the most important aspects of HUB Logistics’ internal logistics.
– We justify our expertise by the fact that our team has done a huge amount of internal logistics outsourcing. We have experience behind us for a long time and we have constantly received more fresh and excellent professionalism from outside the house. We have also been praised for being infinitely flexible at the organizational level.
– Systems and software are essential in material and information management. Of course, others have systems and tools as well, but the important thing is their correct application and utilization. It only comes through strong experience.
According to Mikko Heinilä, Customer satisfaction is the goal even through our own strategy, and it starts from understanding the customer’s goals and planning solutions together.
– It is communication and joint development. And we have succeeded in that, because the customers are really satisfied with us, says Mikko Heinilä.
Have you read our article yet on the business benefits of inbound logistics? If not, you can find the article here.
Learn more about our internal logistics services!
The development of internal logistics and outsourcing respond to these problems
- There are challenges in the production of final products
- Delivery punctuality suffers
- Inventory balances do not match
- Assemblers have wasted time, searching and waiting
- Transparency or lack thereof/opacity
- Skilled personnel spend working time looking for and rummaging through things instead of inefficiently productive work
- The actual costs of internal logistics have not been mapped
- The work is messy and problems are easily repeated
- Staff workloads are uneven
- Not focusing on what you should