Forklift automation in HUB logistics’ Vantaa logistics center has been successfully put into use. HUB logistics’ Development Director Anssi Tura was responsible for the project, which was carried out smoothly together with Toyota Material Handling Finland Oy and Consafe Logistics Oy. Automation brings efficiency, safety and also cost savings to the everyday life of the logistics center.
The logistics industry has gone through significant changes as technology has developed. One of the development steps has been the rise of forklift automation. Automatic forklifts have gradually found their place in the operating environments of warehouses and factories, bringing with them both efficiency and safety.
For HUB, investing in forklift automation was a clear strategic choice. According to Development Director Anssi Tura, HUB logistics has been at the frontline of experimenting with different technologies throughout its history.
– Investing in forklift automation is a clear indication that we have the willpower to develop logistics. At the Hakkila logistics center, we were the first Finnish 3PL operator to use shuttle warehouse automation. Now we are the first operator in Finland to use an AGV forklift in a 3PL multi-customer warehouse.
With the help of an AGV forklift, some of the straightforward functions of storage are transferred to automation. The first task of the automatic forklift truck is to move EUR and FIN pallets from the reception to the high storage shelf positions, controlled by the Astro WMS® warehouse management system.
– We start with one device, but it is possible to expand the use of automation in the future. We looked at the whole more broadly than just one function, and for example the routing in the logistics center is designed in such a way that two forklifts can pass each other.
We are the first operator in Finland to use an AGV forklift in a 3PL multi-customer warehouse.
Anssi Tura, Development Director
Forklift automation in the logistics center brings advantages from many angles
Although the introduction of forklift automation requires initial investment, in the long run it can save you a lot of money. Business Development Manager Petri Lindfors, who was involved in the project from Toyota Material Handling Finland, says that reduced errors and improved efficiency bring significant savings.
– One of the biggest advantages of forklift automation is its ability to improve logistics efficiency and productivity. Automatic forklifts can work without interruption around the clock without the need for breaks, which increases work efficiency. They also optimize their routes and speed up the movement of goods in the warehouse, reducing the time and resources previously spent on manual forklift operations.
According to Lindfors, the operation of automatic forklifts is based on precise specifications, which reduces the number of human errors. This, in turn, leads to more accurate and reliable inventory management and reduces damage and loss of goods.
– People are prone to mistakes, and in the logistics industry mistakes can be expensive. With forklift automation, errors practically go to zero. The device itself doesn’t do fool things, but performs things that people have decided in advance.
Anssi Tura says that approximately 130 transfers per day are made with forklift automation in the logistics center. With the transfers that AGV is now replacing, there would probably be a human-made shelving mistake every four days. According to Tura, there should be no shelving mistakes with forklift automation.
Savings are also created through lower damage costs, because automatic forklift trucks crash very rarely. They are equipped with safety features with safety scanners that ensure the forklift slows down and stops before an obstacle is detected.
Anssi Tura sees that forklift automation offers HUB many advantages.
– It improves efficiency, reduces errors, increases safety and offers flexibility. This technological development is changing the way our processes are managed, allowing for a more efficient use of resources. It opens up opportunities to develop the workforce. Forklift automation is not only a technological change, but it is a clear strategic investment in better and more efficient logistics.
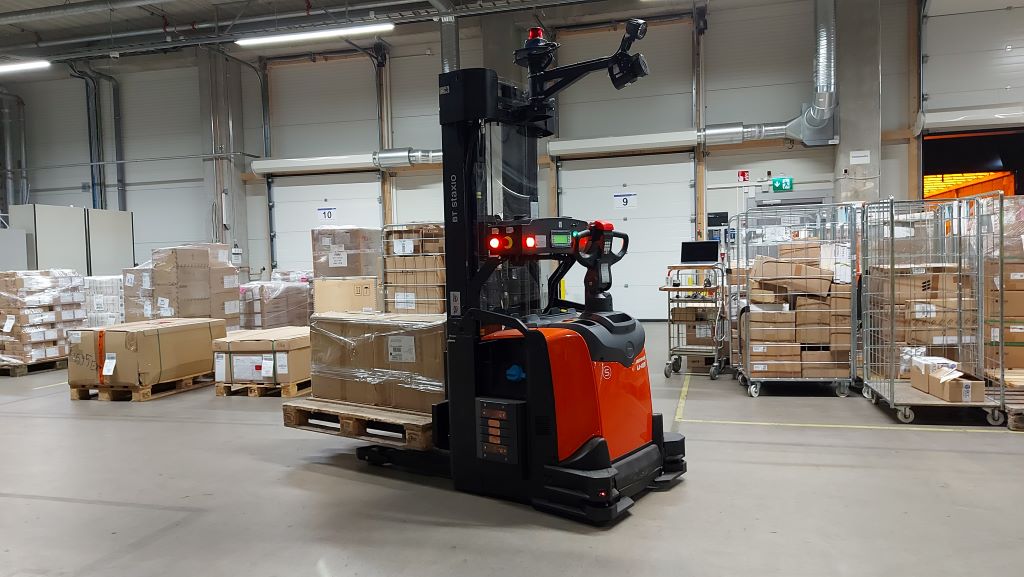
Automation enables more efficient use of labor and increases work safety
Petri Lindfors says that as equipment suppliers, they come across a false image of automation as a substitute for labor.
– Automation cannot replace human expertise. On the contrary, labor can be used more strategically. Manual forklift drivers can focus on more complex tasks such as inspecting goods, quality control and design work. I recently came across an article in which it was said that companies investing in robotics and automation need more employees for, for example, development tasks.
Tura emphasizes that taking care of occupational safety and well-being is very important to HUB logistics.
– By transferring repetitive and body-straining work tasks to be performed by automation, we reduce the heavy lifting tasks performed by the staff. Automation enables us to offer our employees new tasks and develop job descriptions.
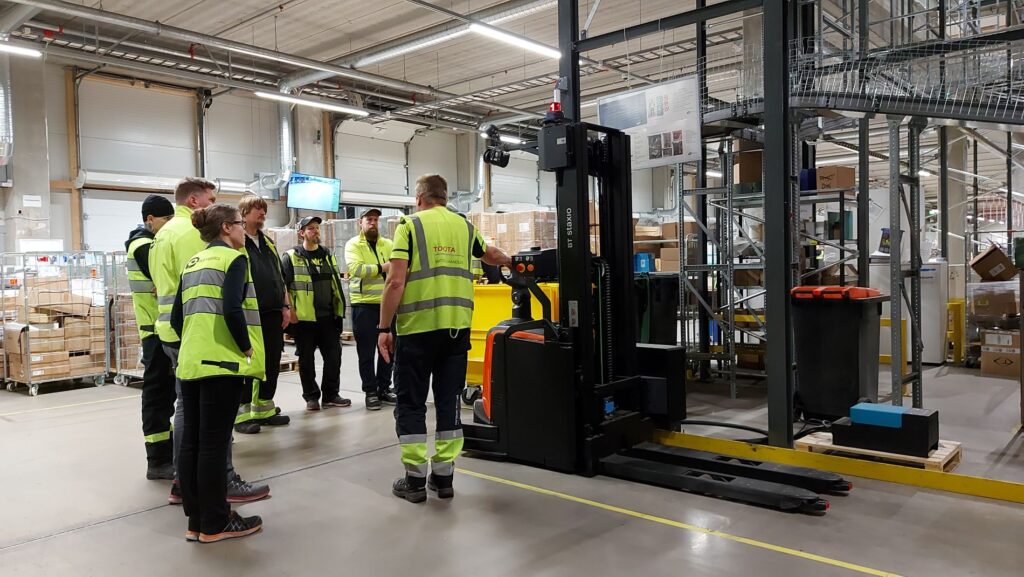
System integrations are an essential part of the successful implementation of forklift automation
In system integrations, data transmission is key to the automatic forklift being able to move correctly. In the AGV project, Consafe Logistics was responsible for planning system integrations in the environment of the Astro WMS® warehouse management system. According to Consafe’s Solution Consultant Maarit Korhola, the three most important things for a successful implementation are sufficient resources, sufficient testing and a comprehensive pre-study.
– The role of the pre-study in a project like this cannot but be emphasized. It should have the right resources available to each party so that the study becomes sufficiently comprehensive. Pre-study creates the basis for everything to be done, starting with what the project’s goal is and the customer’s needs.
– Even in the preliminary plan, we think about what errors and failure situations may occur in the use of AGV and how to deal with them. We go through identified error situations that people can make in current processes, such as leaving a pallet in the wrong place.
Korhola says that almost always something comes up that has not been taken into account. Therefore, along with advance planning, testing is a key factor in a successful project.
– A sign of good testing is that there are new failure situations during the tests. It tells you that more than happy flow has been tested, i.e. whether the process is going as planned without any disruption at any stage of the process. If something is accidentally done wrong in the tests, it is likely that the same error would show up in production. I would be worried if no errors appeared during testing. Through tests, we can correct malfunctions and errors before transferring to production.
Implementation to the finish line with good cooperation and smooth communication
In addition to careful planning, the effective implementation of forklift automation requires smooth cooperation and communication between different stakeholders, as well as continuous monitoring. This ensures that forklift automation brings desired benefits to improve efficiency and accuracy in warehouse operations.
Maarit Korhola of Consafe is satisfied with the implementation of the project with all parties involved. She says that cooperation and discussions were of high quality. Clear communication helped the project to go through.
Development director Anssi Tura says that the long cooperation with Consafe moved the project forward rapidly.
– Our processes are familiar to Consafe, so they were able to design on familiar ground. The know-how of their automation team and examples of similar projects enabled us to find the best possible solution.
Toyota Material Handling’s Petri Lindfors also thanks the smooth progress of the project.
– The definitions were made well and in good agreement. The system supplier cannot do the project alone, but requires sufficient resources from all the stakeholders affected by the project. This was our first project in Finland where a warehouse control system was made and put into use. An extremely good additional lesson for the future.
According to Anssi Tura, a large automation project requires a great investment and commitment from all parties, so that the project can be carried out according to the planned schedule.
– I want to thank both partners. It was a pleasure to be involved in this project. Now the actual use begins and I am looking forward to what kind of data we will get in the future about the functionality of the automation and the benefit it brings.
Further information:
HUB logistics Finland Oy
Anssi Tura, Development Director
anssi.tura@hub.fi
Toyota Material Handling Finland Oy
Petri Lindfors, Business Development Manager
petri.lindfors@fi.toyota-industries.eu
Consafe Logistics Oy
Maarit Korhola, Solution Consultant
maarit.korhola@consafelogistics.com
Further reading:
HUB logistics warehousing services
Hakkila logistics center: 3PL-automated warehouse